Überwachung von Motoren/Generatoren durch Strom-/Spannungsanalyse
Produktbezeichnung: e-MCM
Wie funktioniert die Technologie und was kann Sie leisten?
Die patentierte Technologie verwendet einen modellbasierten Spannungs- und Stromsystemansatz, um eine Vielzahl von Fehlern an Elektromotoren zu erkennen.
Komponentenfehler
- Lose Fundamente/Komponenten
- Mechanische Unwucht
- Fehlausrichtung
- Transmission Fehler
- Fehler im angetriebenen Gerät
- Getriebe, Riemen, Kupplung
- Lagerschäden
- Stator- und Rotorfehler
- Interne elektrische Fehler
- Externe elektrische Störungen
Prozessfehler
- Hohe Energieaufnahme
- Schlechter Wirkungsgrad
- Kavitation in Pumpen
- Strömungsturbulenzen in Ventilatoren, Gebläsen
- Filter- und Wärmetauscherverschmutzung
- Schmierung
- Überdimensionierte/unterdimensionierte Motoren
- Störung der Luftströmung
Elektrische Fehler
- Vr, Vs und Vt
- lr, Is und It
- Frequenz
- Spannungs-unsymmetrie
- Strom-unsymmetrie
- Motorlast
- Leistungsfaktor
- Wirkleistung
- Blindleistung
- Oberschwingungen
Dieser modellbasierte Ansatz funktioniert nach dem Prinzip, dass der von einem Elektromotor aufgenommene Strom nicht nur durch die angelegte Spannung, sondern auch durch das Verhalten sowohl des Motors als auch des angetriebenen Geräts beeinflusst wird. Dadurch werden die Verzerrungen der Stromverläufe identifiziert, die nicht durch Verfälschungen des Spannungsverlaufs verursacht wurden und daher durch das Verhalten des Systems aus Motor und angetriebenen Geräten verursacht worden sein müssen. Die Frequenz dieser Verfälschungen gibt die Art der Ursache an, und das Ausmaß der Verfälschungen gibt den Schweregrad der Ursache an.
Benutzerfreundlichkeit
Herkömmliche Zustandsüberwachungssysteme sind zwar hervorragend in der Lage, Daten zu sammeln, erfordern aber viel Fachwissen, um sie in verwertbare Aussagen umzuwandeln - genau der Teil, den Sie wirklich brauchen. Das e-MCM ist in der Lage, sein durch den Selbstlernprozess aufgebautes Wissen über Ihre Maschinen zu nutzen, um nicht nur zu erkennen, wann sich ein Fehler entwickelt, sondern auch die Art des Fehlers zu erkennen. Dadurch kann das Wartungsteam seine Maßnahmen genau auf den richtigen Bereich konzentrieren, ohne auf die Unterstützung durch einen Diagnoseexperten angewiesen zu sein.
Das Diagnosesystem ist in der Lage, die meisten der üblichen mechanischen Fehler zu erkennen, die bei typischen elektromotorisch angetriebenen Geräten auftreten, von Unwucht und Fehlausrichtung bis hin zu Lagerproblemen. Da e-MCM durch die Messung des vom Elektromotor aufgenommenen Stroms und der Spannung arbeitet, kann es darüber hinaus auch Probleme mit dem Elektromotor selbst diagnostizieren sowie einen Einblick in die Prozessbedingungen und das Potenzial zu deren Optimierung auf der Grundlage von Leistung, Phasenwinkel und Gesamtoberwellenverzerrung geben.
Übersichtliche Berichterstellung
Korrekturmaßnahmen. e-MCM erfordert nur dann Aufmerksamkeit, wenn es ein Problem erkennt. Das macht es sehr attraktiv im Vergleich zu Walkaround-Systemen, die erheblichen Aufwand und Kosten erfordern, nur um herauszufinden, ob ein Problem besteht oder nicht. e-MCM bewertet automatisch den Schweregrad aller Abweichungen vom Normalbetrieb und vermittelt dem Benutzer die Ergebnisse der ausgefeilten Analyse in einer einfachen, überzeugenden Ampelanzeige. Sobald ein Fehler voranschreitet, wechselt die Ampel von grün auf gelb und zeigt damit an, dass in Zukunft Wartungsmaßnahmen erforderlich sind. Eine Ampel zeigt an, dass der Schweregrad des Problems eine sofortige Maßnahme erfordert.
Installation
Einfache Installation
e-MCM benötigt zur Installation nur drei einfache Stromwandler und einen Abgriff der Spannungen.
Echtzeit-Überwachung
e-MCM nimmt ständig Messungen vor und vergleicht sie mit dem Referenzzustand, um den Schweregrad und die Art eines sich entwickelnden Fehlers zu beurteilen. Das Gerät ist in der Lage, Anomalien in einer Vielzahl von Betriebszuständen zu erkennen, und es ist sogar in der Lage, seinen Selbstlernprozess zu erweitern, wenn es erkennt, dass es seine ursprünglichen Einlerngrenzen überschritten hat. Dadurch kann e-MCM eine sehr empfindliche Fehlererkennung ohne Fehlalarme.
Erleichterte Wartungsplanung
Fernüberwachungs- und Berichterstattungsdienste tragen zur Entwicklung eines nachhaltigen vorausschauenden Instandhaltungssystems (PdM) in der Anlage bei, ohne dass die Besatzung zusätzliche Arbeitsbelastung auf sich nehmen muss.
Schaltschrankeinbau
Ein eMCM System besteht aus einem externen Display zur Montage in der Schaltschranktür und einem Hutschienenanalysegerät. Das externe Display wird per Kabel mit dem Analysegerät verbunden.
Der direkte Vergleich.
Vergleich: Vibrationsanalyse Vergleich: MCSA
Wie verhält sich die modellgestützte Spannungs- und Stromsystemanalyse im Vergleich zur Vibrationsanalyse?
Im Vergleich zur Schwingungsanalyse ist die e-MCM-Technologie empfindlicher gegenüber Torsionsphänomenen, während Schwingungssysteme empfindlicher gegenüber radialen Phänomenen sind. Das modellbasierte System kann ein breites Spektrum mechanischer Phänomene innerhalb des Motors und der angetriebenen Ausrüstung erkennen, nicht nur in Bezug auf Lager, sondern auch auf allgemeine Probleme wie Fehlausrichtung und Unwucht. Es erkennt auch eine Reihe von elektrischen Problemen, wie z.B. gebrochene Rotorstäbe und lose Motorwicklungen.
Die modellbasierte Spannungs- und Stromanalyse misst eine Reihe von elektrischen Parametern wie die gesamte harmonische Verzerrung (THD), Spannungsungleichgewicht und Stromungleichgewicht, die ihrerseits zu längerfristigen mechanischen wie auch elektrischen Problemen beitragen können. Diese Parameter können auch zu Schwingungssignalen führen, die von der Schwingungsanalyse manchmal als mechanische Fehler wie z.B. Lagerprobleme fehlinterpretiert werden können. Da diese elektrischen Parameter direkt von der Technologie gemessen werden, können solche Fehldiagnosen vermieden werden.
Wie bei der Schwingungsüberwachung nehmen die durch den modellbasierten Systemansatz identifizierten Signale zu, wenn die Anlage unter größerer Belastung arbeitet. Allein aus den erhöhten Schwingungspegeln könnte man fälschlicherweise den Schluss ziehen, dass ein Problem entstanden ist. Da modellbasierte Systeme Spannung und Strom messen, berechnen sie auch die Leistung und verwenden diese Lastinformationen zur Normalisierung der Messwerte, um solche Fehldiagnosen zu vermeiden.
Funktion/Problem | Eignung von Beschleunigungssensoren | Eignung von e-MCM |
Unwucht | ++++ | ++ |
Fehlausrichtung | ++++ | ++++ |
Lose Teile | ++ | +++ |
Anstreifen | ++ | ++++ |
Wälzlagerdiagnose | ++++ | ++++ |
Gleitlagerdiagnose | ++ | +++ |
Turbulenz in Strömungen | + | +++ |
Kavitation | +++ | ++ |
interne Korrosion | o | ++ |
Riemenantrieb | + | ++++ |
o = sehr ungeeignet / + = geignet / ++ = gut geignet / +++ = sehr gut geignet / ++++ = perfekt geignet
Wie schneidet die modellbasierte Spannungs- und Stromsystemanalyse im Vergleich zu MCSA ab?
MCSA (Motor Current Signature Analysis) ist eine gut etablierte Technik, die auf dem gleichen Grundprinzip wie die modellbasierte Spannungs- und Stromanalyse beruht, nämlich dass der von einem Motor aufgenommene Strom von einer Reihe von Faktoren beeinflusst wird, die jeweils bei bestimmten, identifizierbaren Frequenzen auftreten. Die MCSA wird klassischerweise zur Identifizierung von Rotorstabproblemen in Induktionsmotoren verwendet, ein Phänomen, das mit modellbasierten Systemen ebenfalls identifiziert werden kann, wobei die Auflösung im Allgemeinen besser ist als bei der MCSA. Allerdings ist das modellbasierte System bei der Identifizierung und Diagnose eines breiten Spektrums von Phänomenen wesentlich leistungsfähiger als MCSA.
Es gibt wichtige Unterschiede zwischen der Technologie und MCSA-Systemen
- MCSA führt eine Spektralanalyse des vollen Motorstroms durch, der von der 50-Hz- oder 60-Hz-Versorgungsfrequenz dominiert wird
- Rotorstabfehler werden als Höhenunterschied zwischen der Spitzenfrequenz der Versorgungsspannung und der poldominanten Durchlassfrequenz erkannt, wobei typischerweise 60 dB für einen Motor in gutem Zustand auf 30 dB fallen, was sehr schlecht ist
- MCSA basiert im Allgemeinen nur auf Strom
- MCSA verwendet oft nur eine Phase
Spezifikation und Umfang des Artesis Online Condition Monitoring e-MCM
Die Artesis-Online-Überwachungstechnologie liefert Diagnose- und Prognose-Daten (Zeit bis zum Ausfall) von Drehstrom-Asynchronmotoren, angetriebenen Geräten wie Pumpen, Lüftern und Kompressoren, Förderanlagen, Kühlern und Mischern über die dreiphasige Spannungs und Strommessung. Die Online-Überwachungstechnologie von Artesis nutzt einen intelligenten, modellbasierten Ansatz zur Erkennung von Anomalien durch Messung der Strom- und Spannungssignale der Stromversorgung des Motors. Die Technologie ist in der Lage, die Daten kontinuierlich zu überwachen und zu protokollieren, um eine Fehlerursachenanalyse durchzuführen. Darüber hinaus teilt sie dem Endnutzer die Fälligkeitstermine für Wartungsmaßnahmen mit, was eine wichtige Information für die Wartungsplanung ist.
Der Umfang des Artesis Online Monitoring Solutions umfasst 7 verschiedene Faktoren. Diese Faktoren sind wie folgt aufgelistet: Software, Hardware, Erklärungen zur Methode der Online-Überwachung, Schulung, Software-Updates, MCC-Panel & Kommunikationsverbindungen und Einschränkungen der Technologien.
Die Sprache der Software ist Englisch (Deutsch ist in der Umsetzung). Die Software ist in der Lage, 24/7 eine kontinuierliche Überwachung und Diagnose von elektrischen und mechanischen Fehlern durchzuführen
Die Artesis-Software ist in der Lage, dem Endbenutzer Informationen über die Zeit bis zum Ausfall zu liefern, die für die Wartungsplanung der erkannten Fehler verwendet werden können, wobei automatisch ein Arbeitsauftrag generiert wird. Die Parameterdaten der überwachten Anlage werden protokolliert, um sie für die Fehlerursachenanalyse zu nutzen. Durch den Vergleich des ursprünglichen Motorzustands mit der umfangreichen Datenbank wird der ursprüngliche Fehlerzustand ermittelt.
Die Artesis-Software kann den Motor als effektiven Sensor nutzen, ohne dass zusätzliche Spezialsensoren erforderlich sind. Sie behandelt jeden Betriebspunkt des Motors als einen Cluster im dreidimensionalen Raum (Leistungsfaktor, Verstärkung, Netzfrequenz). Jedes Cluster hat ein eigenes Modell.
Die Überwachung und der Verlauf der folgenden Parameter im zeitlichen Verlauf können über die Trendgrafiken der Software angezeigt und gespeichert werden:
- Loses Fundament/Bauteile
- Unwucht/Ausrichtung/Kupplung/Lager
- Rotor
- Stator/Kurzschluss
- Interne elektrische Fehler
- Externe elektrische Fehler
- Fehler in der elektrischen Versorgung
- Fehler aufgrund von Lastschwankungen
- Dreiphasenstrom (jedes Phasensignal)
- Dreiphasige Spannung (jedes Phasensignal)
- Wirkleistung
- Blindleistung
- Gesamter Wirkleistungsverbrauch (kWh)
- Gesamtblindleistungsverbrauch (kVArh)
- Täglicher Gesamtwirkleistungsverbrauch (kWh)
- Täglicher Gesamtblindleistungsverbrauch (kVArh)
- Gesamt-Wirkleistungsaufnahme des Vortages (kWh)
- Gesamtblindleistungsaufnahme des Vortages (Kvarh)
- Betriebsstunden gesamt (HH:MM)
- Letzte laufende Stunde (HH:MM)
- Last (%)
- Leistungsfaktor
- Spannungsunsymmetrie (%)
- Stromunsymmetrie (%)
- Frequenz (Hz)
- Gesamte harmonische Verzerrung
- 3. Oberschwingung
- 5. Oberschwingung
- 7. Oberschwingung
- 9. Oberschwingung
- 11. Oberschwingung
- 13. Oberschwingung
Die Software ist in der Lage, Berichte über die überwachten Anlagen zu erstellen. Der Bericht enthält den Zustand der Anlage, vorhandene und entstehende mechanische und elektrische Fehler. Die Endbenutzer können per E-Mail über die Fehlermeldungen informiert werden.
Die Software ist in der Lage, den Endnutzern die PSD-Signale (Power Spectrum Density) der überwachten Geräte zu liefern.
Die Software unterstützt OPC Server und Modbus TCP/IP.
Die Software sollte mit e-MCMs kommunizieren, ohne dass eine statische IP erforderlich ist.
Gemessene und berechnete Daten werden über das Datenbankmanagementsystem MSSQL/MSSQL Express protokolliert.
Tägliche und stündliche Berichte über den Stromverbrauch und Trendanalysen.
Das Datenbanknetzwerk ist von anderen Datenbanksystemen aus zugänglich.
Mindestanforderungen für den Master-PC (auf dem die Software von e-MCM läuft)
- Desktop-PC oder Industrie-Touch-PC
- Prozessor: PC i5, 2 GHz
- Arbeitsspeicher: 8 GB
- Festplattenspeicher: 1 TB
- Grafikkarte: SVGA 1024 x 768 (oder höher)
- Betriebssystem: Windows 10 PRO 64bit
e-MCM Datenerfassungsgerät
- Das Gerät wird mit AC- und DC-Netzteilen betrieben. Versorgungsspannung: AC100~240V/ DC120-370V
- Das Gerät ermöglicht die Konfiguration und Überwachung elektrischer Parameter vor Ort, ohne dass eine Software oder ein PC mit einem mindestens 4-Zoll-Display erforderlich ist.
- Das Gerät ist mit Direktmotoren, Softstartern und VFD-Motoren kompatibel.
- Das Gerät ist in der Lage sein, ohne einen Konverter mit einem TCP/IP-Server zu kommunizieren
Ein e-MCM-Online-Zustandsüberwachungssystem (CM) ermöglicht eine kontinuierliche Überwachung des Betriebszustands des Motors.
Dieses prädiktive Überwachungssystem arbeitet mit einer modellbasierten Fehlererkennungsmethode (MBFD), die eine Erkennung und Diagnose von Fehlern im Motor ermöglicht.
Das System ist in der Lage sein, Anomalien zu erkennen, indem es die Wellenform der Spannungs- und Stromsignale der dreiphasigen Stromversorgung des Motors misst. Das System liefert eine rechtzeitige Warnung über die Diagnose- und Prognoseinformationen (Zeit bis zum Ausfall) des Motors.
Das E-MCM-System ist in der Lage sein, Fehler bei variablen Frequenzen nur bei Niederspannungsanwendungen zu analysieren.
Das E-MCM-System besteht aus einem primären E-MCM-Analysator mit Spannungs- und Stromsensorenkabel für jeden Motor und einem Industriecomputer mit Human Machine Interface (HMI), der auch als Webserver dient. Alle E-MCM-Analysatoren werden mit diesem Computer vernetzt.
Das System ist in der Lage sein, Anomalien zu erkennen, indem es die Wellenform der Spannungs- und Stromsignale aus der dreiphasigen elektrischen Versorgung des Motors misst. Die Analyse wird in jedem ECM-Analysator im Frequenzbereich mit Datenanalyse durchgeführt, um die mit den harmonischen Frequenzkomponenten verbundenen Grundursachen zu ermitteln.
Dieses System arbeitet unabhängig und sendet über ein festes Kabel ein spannungsfreies Kontaktalarmsignal an die vorhandene SPS/SCADA für jegliche Anomalien des Systems selbst und/oder der zu überwachenden Ausrüstung.
Der Auftragnehmer stellt die erforderliche Schnittstelle zur bestehenden SPS/SCADA bereit, einschließlich Verkabelung und Änderung der bestehenden SCADA-HMI-Seiten zur Anzeige des Alarms/Ereignisses.
Der Auftragnehmer muss die Lernphase des Systems definieren und als Teil der Installationsphase betrachten. Die komplette Lernphase des e-MCM wird ca. 7-10 Tage nach der Inbetriebnahme dauern, und die Lernphase besteht aus zwei Phasen
- Lernphase, in der Artesis e-MCM die Signale klassifiziert und keine Überwachung vornimmt.
- Verbesserungsphase, in der Artesis e-MCM mit der Überwachung beginnt und auch das mathematische Modell (das in der ersten Phase erstellt wurde) mit neuen Daten aktualisiert. Nach der Lernphase wird der erste Bericht über die AESViewer Software / Cloud Interface präsentiert.
Das System muss in der Lage sein, die Daten kontinuierlich zu überwachen und zu protokollieren, um eine Fehlerursachenanalyse durchführen zu können, und es muss so konzipiert sein, dass es die folgenden Arten von Fehlern minimal erkennt und anzeigt:
- Gebrochener oder beschädigter Rotorstab
- Falsche Ausrichtung oder Unwucht des Rotors
- Lockerung des Fundaments
- Defekte Lager
- Ausfall der Pumpenkupplung und der mechanischen Last
- Hintergrundschwingungen
- Probleme mit der angetriebenen Last, wie z. B. Schäden an den Ventilatorflügeln, lockere Riemen, Zahnradschäden, Unwucht der Getriebewelle und lokale Lagerprobleme.
Das E-MCM-System erzeugt mindestens die folgenden Berichte:
- Gesamtübersicht über die Leistung aller überwachten Motoren
- über die Leistung eines einzelnen Motorsatzes
- Zusammenfassender Bericht für alle kritischen Spannungs- und Stromparameter
- Nominale, durchschnittliche, minimale und maximale Spannung und Stromstärke
- Durchschnittlicher Leistungsfaktor
- Durchschnittliche Wirkleistung
- Durchschnittliche harmonische Gesamtverzerrung
- Bericht über die Betriebsdauer aller Motoren
- Der e-MCM-Analysator, der Industriecomputer und die Mensch-Maschine-Schnittstelle müssen in einem Schaltschrank mit unterbrechungsfreier Stromversorgung (USV) untergebracht sein. Die USV muss eine Backup-Kapazität von mindestens einer Stunde haben.
- Das System ist in der Lage sein, die Daten kontinuierlich zu überwachen und zu protokollieren, um eine Fehlerursachenanalyse durchführen zu können, und es ist so konzipiert, dass es minimal die folgenden Fehlertypen erkennt: Stator-, Rotor-, Lager-, Maschinen-, Getriebe- und Prozessfehler
- Stator Fehler
- Interturn-Kurzschluss (die frühe Phase des Turn-to-Turn-Kurzschlusses)
- Phase-Phase-Kurzschluss
- Impedanzunsymmetrie oder -verschiebung
- Verschlechterung der Isolation
- Weicher Fuß (Statorverformung)
- Loser Fuß (Schraube locker)
- Überhitzung der Wicklung
- Lockerheit der Wicklung
- Lockerung der Lamellen
- Rotor Fehler
- Unwucht (Lüfter, Wellenverformung)
- Thermischer Bogen (Unwucht)
- Statische und dynamische Exzentrizität
- Reibung
- Starke Porosität
- Winkelfehler und Parallelversatz
- Gebrochene, beschädigte und lose Rotorstäbe
- Überhitzung
- Lockerheit der Wicklung
- Lockerung der Lamellen
- Degradierung des Dämpfungskäfigs
- PM-Verschlechterung
- Lagerung
- Grübchenbildung am Außen- und Innenring
- Kugel-/Rollenverschleiß
- Verformung des Käfigs/der Laufbahn
- Verkantetes Lager
- Kriechen/Schleudern des Lagers
- Falsches und echtes Brinelling
- Gleitlagerölwirbel und -peitschen
- Radiale Vorspannung des Gleitlagers
- Reibung des Rotors im Gleitlager
- Maschinen Fehler
- Grübchenbildung am Außen- und Innenring
- Kugel-/Rollenverschleiß
- Verformung des Käfigs/der Laufbahn
- Verkantetes Lager
- Verunreinigung des Schmierfetts
- Überfettung
- Kriechen/Schleudern des Lagers
- Falsches und echtes Brinelling
- Gleitlagerölwirbel und -peitschen
- Radiale Vorspannung des Gleitlagers
- Reibung des Rotors im Gleitlager
- Fehler in der Übertragung
- Abgebrochene Zähne/Klauen
- Lockerheit
- Übermäßiges Spiel
- Exzentrizität
- Unwucht
- Qualität der Maschen
- Flankenspiel
- Fluchtungsfehler
- Probleme in der Montagephase
- Prozessfehler
- Hoher Energieverbrauch
- Niedriger Wirkungsgrad
- Kavitation in Pumpen
- Strömungsturbulenzen in Ventilatoren, Gebläsen
- Verschmutzung von Filtern und Wärmetauschern
- Schmierung
- Überdimensionierte/unterdimensionierte Motoren
Das E-MCM-System sollte in der Lage sein, die Verteilung aller drohenden Fehler mit ihren Schweregraden anhand eines Balkendiagramms in einer grafischen Darstellung anzuzeigen. In derselben grafischen Darstellung sollte es Betriebsbereiche geben, die den Schweregrad jedes Fehlers und die geschätzte Zeit für die Einleitung von Abhilfemaßnahmen zur Behebung der Ursache vor einem Motorausfall angeben. Einzelheiten zu den korrelierten Informationen zwischen den Betriebsbereichen, der Beschreibung und der Entscheidungshilfe sind in der Tabelle auf der nächsten Seite aufgeführt.
Betriebsbereich | Beschreibung | Zeitrahmen für Abhilfemaßnahmen |
Grün | Motor läuft einwandfrei Motor | weiter überwachen |
Gelb | Motor entwickelt Probleme | 6 Monate, Überwachung beenden und Untersuchungsmaßnahmen einleiten |
Rot | Das Problem ist schwerwiegend und der Motor fällt aus | 1 Monat, den Betrieb der Pumpe einstellen und sofortige Maßnahmen ergreifen |
Das E-MCM-System sollte so konzipiert sein, dass es die folgenden Berichte erstellt:
- Allgemeiner Zustandsbewertungsbericht, der einen Gesamtüberblick über die Leistung aller zu überwachenden Motoren gibt
- Leistungsbericht der einzelnen Motoren, der die Verteilung aller drohenden Fehler, den Schweregrad und die Betriebsbereiche anzeigt.
- Ein zusammenfassender Bericht für alle kritischen Spannungs- und Stromparameter, einschließlich:
- a. Nenn-, Durchschnitts-, Mindest- und Höchstspannung und -strom
- b. Durchschnittliche Unsymmetrie für Spannung und Strom
- c. Durchschnittlicher Leistungsfaktor
- d. Durchschnittliche Wirkleistung
- e. Durchschnittliche harmonische Gesamtverzerrung
- Bericht über die Betriebsstunden aller Motoren über Fernzugriff auf die Web-Basis mit IoT Online Cloud
- Mindestens 10 ausgewählte Mitarbeiter sollen in der Lage sein, E-Mail-Benachrichtigungen zu erhalten und diese Berichte über den Fernzugriff auf die Datenbank über die Tablets oder PCs der Beamten einzusehen.
Jeder E-MCM-Analysator weist potenzialfreie Kontakte für eine direkte digitale Schnittstelle zur speicherprogrammierbaren Steuerung (SPS) oder zur Remote Terminal Unit (RTU) des Anlagenprozesses auf, um die Übertragung von Alarmen an das SCADA-System zu ermöglichen. Zwischen dem E-MCM-System und der SPS/RTU, die an ein SCADA- oder Telemetriesystem angeschlossen ist, ist keine Datenschnittstelle zulässig
Bei Erkennung einer Anomalie an einem in Betrieb befindlichen Motor sendet das E-MCM-System über die angeschlossene SPS/RTU einen Alarm an das SCADA, um den Bediener zu alarmieren und eine E-Mail-Warnung an die ausgewählten Mitarbeiter zu senden. Nach Erhalt der E-Mail-Warnung muss der Mitarbeiter über sein Mobiltelefon oder Tablet einen Fernzugriff auf das E-MCM-System durchführen, um die im E-MCM-System erfassten detaillierten Diagnoseinformationen zu prüfen.
Der E-MCM-Analysator, der Computer und die Mensch-Maschine-Schnittstelle sollen in einem Schaltschrank untergebracht werden. Es wird empfohlen, dass das gesamte E-MCM-System die Stromversorgung aus dem bestehenden unterbrechungsfreien Stromversorgungssystem (USV) in der Nähe des Prozesses/der Anlage bezieht. Die Schalttafel muss für eine Zwangsbelüftung ausgelegt sein, die ausreicht, um die von allen in der Schalttafel untergebrachten Geräten erzeugte Wärme abzuführen.
Der Auftragnehmer muss alle Inbetriebnahmetests durchführen, einschließlich einer Simulation, die sicherstellt, dass der E-Mail-Alarm alle ausgewählten Beamten erreichen kann, und er sollte die Kommunikation des SCADA-Systems für die Alarmmeldungen sicherstellen und simulieren.
Der Auftragnehmer muss ein Anwendungsprogramm für die PCs oder Tablets der Mittarbeiter bereitstellen. Das Anwendungsprogramm soll den Beamten den Fernzugriff auf den E-MCM-Server ermöglichen, um Leistungs- und Wartungsinformationen, Berichte usw. für alle Motoren abzurufen.
- Die Schulung wird – optional - von der Herstellerfirma durchgeführt.
- Die Schulung umfasst Informationen über die Software, die Inbetriebnahme, die Fehlersuche und Hilfe bei der Ursachenanalyse.
- Die Schulungsunterlagen werden den Teilnehmern vor der Schulung zur Verfügung gestellt.
- Die Herstellerfirma wird den Master-PC mit der neuesten Version der Software aktualisieren.
- Die Herstellerfirma verpflichtet sich, dass Software-Updates im ersten Jahr nach Inbetriebnahme kostenlos durchgeführt werden. Von da an sind Software-Updates kostenlos. Ab dem zweiten Jahr müssen die Kunden ihre Software selbst aktualisieren.
- Die Software wird mit der neuen Version aktualisiert, ohne dass Daten verloren gehen.
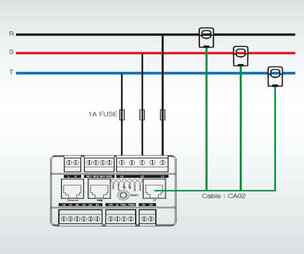
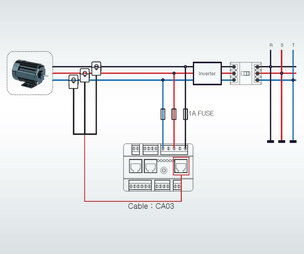
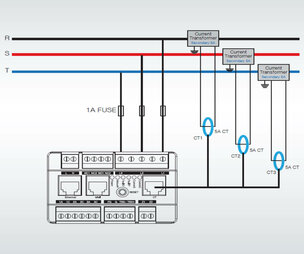
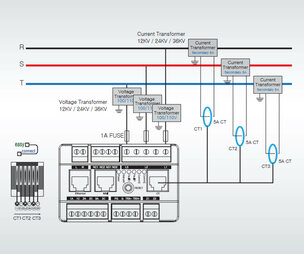
Hinweis zu 6.1.3
Die Spannungs- und Stromanschlüsse müssen an die Kabel zwischen Motor und VFD angeschlossen werden.
Hinweis zu 6.1.4
E-MCM-Spannungseingänge unterstützen bis zu 690 Vrms Phase-Phase-Direktanschluss, Spannungen über diesem Wert sollten über einen Spannungswandler übertragen werden.
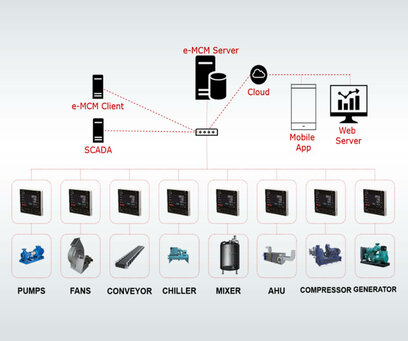

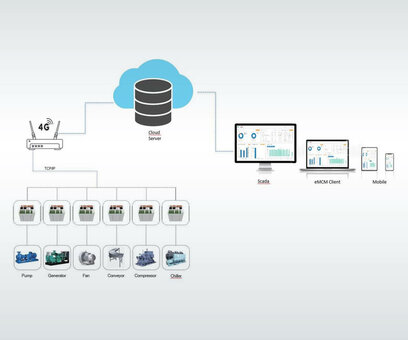
e-MCM Online-Zustandsüberwachungsgeräte sind nur für dreiphasige Wechselstrommotoren anwendbar. Gleichstrommotoren und einphasige Motoren können nicht mit e-MCM überwacht werden. Die unten aufgeführten Kriterien stellen die Einschränkungen des e-MCM Online Condition Monitoring Geräts dar.
No. | Motorparameter | Beschränkungen (falls vorhanden) |
1. | Spannung | Einphasen- und Gleichstrommotoren |
2. | Leistung | Keine Begrenzung |
3. | Strom | ohne Begrenzung |
4. | Umdrehungen | min. 300 rpm |
5. | Frequenz | 20-119 Hz |
6. | Vorhandene PT-Anforderung | Motorspannung > 690 V |
Für jede Projektierung der Artesis Online-Zustandsüberwachungslösung sollte der Endnutzer den Verkäufer mit dem Ausrüstungsinformationsformular (in Anhang 1) in dem von Avibia bereitgestellten Excel-Format informieren.
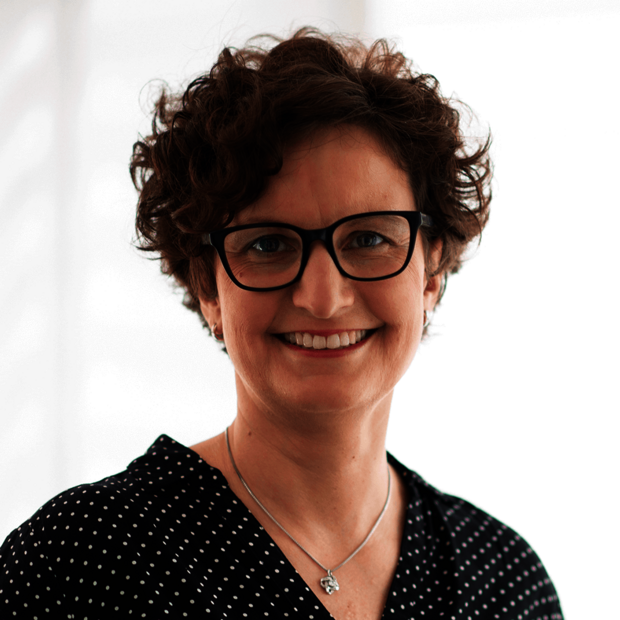
Sie möchten mehr erfahren?
Gerne. Vereinbaren Sie Ihren persönlichen Beratungstermin mit Melanie Peintner.